Two important components of the pellet machine during the use are the roller and the die.
The moving pellet machine means that the main shaft drives the flat die to rotate, and the pressure roller does not move.The moving roller pellet machine means that the main shaft drives the pressing roller to rotate, and the flat die does not move. Moving roll flat die granulator for larger scale pellet production
How to maintain roller and die?
When purchasing a pellet machine, many people will consider whether it is energy saving, size, convenience of movement, and price of pellet machine. As everyone knows, there is one more important thing, that is, the accessories of the feed granulation equipment. According to customer feedback, the cost of accessories per year accounts for nearly 8% of feed equipment costs. Die and rollers are common wearing parts during the use of pellet feeders. When the user finishes using it, it is best to purchase the raw material factory accessories. The following describes some maintenance methods for the die and the roller.
- Regularly refuel the transmission parts of the biomass pellet machine, lubricate the roller bearings every 2 hours, and lubricate the front bearings of the spindle every 4 hours to ensure flexible rotation of the transmission parts of the pellet machine and reduce the working load.
- Regularly replace the lubricating oil in the gearbox of the biomass pellet machine. After the new machine is operated for half a month, the oil needs to be replaced once. After each continuous operation, it must be replaced once for about 1000 hours, which can extend the service life of the gear.
- Once a week, you must carefully check whether the connecting parts of each part are loose, whether the safety switch is reliable, and clean the feeding auger and conditioner to avoid mechanical failure.
- Check the transmission keys and the wear of the hoops every half month, and if found the wear, they should be replaced in time to avoid the ring mold shaking and affect the output.
- Use high quality ring mold, pressure roller. Inferior ring molds with rounded holes and rough inner holes are eliminated, and the compression ratio of the ring mold is selected according to different formulas to ensure smooth discharge of the ring mold, avoiding increased power consumption and reducing production capacity.
- Adjust the gap between the ring die and the press roller for each shift. If the machine is blocked, the pressure roller must be loosened to remove the material of the inner wall of the ring mold and then adjust the gap between the mold rolls. It must not be forced to start, so as to avoid damage to the transmission parts and bearing parts due to severe vibration.
- To prevent overload production. The production process can not exceed the working capacity of the biomass pellet machine itself, otherwise the motor damage and the accelerated wear of the components will occur, shortening the service life of the pelletizer.
- The raw materials must be cleaned and removed, and the iron removal device should be cleaned once every shift to prevent foreign matter from entering the ring mold working chamber, causing the phenomenon of vibration and cracking of the ring mold.
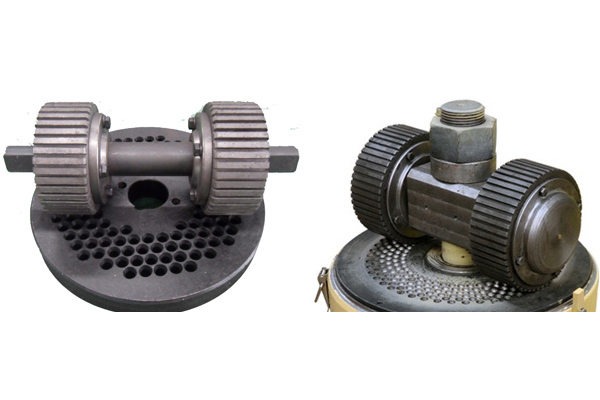
How to reduce the damage of the pellet machine?
The die of the pellet machine should be flipped over with the other side after a period of time. Don't wait until the wear is serious, then turn it over. Especially the thin die should be flipped frequently. It is not good to use both sides or your mold is pressed. If the particles are not hard, they must be processed and refurbished.
Die inspection and maintenance.
Check the die before starting each time to ensure that there are no foreign objects on the grinding disc and the die is not worn. The service life of the die is 300-500 hours under normal operating conditions. After the die is worn, the other side can be replaced (only one side of the die can be used) ).
Pressure roller inspection and maintenance.
Check the pressure roller before each start-up to ensure that no foreign matter hinders the roller from running freely, and check if the pressure roller is worn. The service life of the pressure roller is 300-500 hours under normal conditions. Usually, when the new die is replaced, the pressure roller shoule be replaced together .